Enterprise Resource Planning
About
Who We Are
Our familiarity with the Plex Smart Manufacturing Platform™ comes from many years of using Plex, first as customers and now as partners. Our “Plexperts” have used the platform to support global manufacturing operations and continue to be active contributors to the development of Plex. With a heritage in manufacturing, we have an excellent understanding of the challenges manufacturers face and have successfully provided technical solutions to drive continuous improvement.

Team Facts
-
Our team is fully accredited in the Plex implementation process.
-
We have offices both in Mexico and the US with bilingual resources.
-
Our team turnover rate is nearly 0%
-
We employ engineers, supply chain experts, CPAs, Six Sigma Black Belts, EDI experts, and IT experts on our team.
Engagement
Our value outcome approach includes:
-
An IT evaluation.
-
Process mapping.
-
Industry expertise.
-
Infrastructure diligence.
-
Cybersecurity readiness.
-
Compliance consultants.
-
Project accountability.
-
Proactive budget management.
About Plex
Plex Systems, Inc.® delivers the first smart manufacturing platform that empowers the world’s leading innovators to make awesome products. Built in the cloud, the Plex Smart Manufacturing Platform gives manufacturers the ability to drive true business transformation by connecting, automating, tracking, and analyzing every aspect of their business. The Plex Smart Manufacturing Platform includes MES, ERP, supply chain planning, Industrial IoT and analytics to connect people, systems, machines, and supply chains, enabling them to lead with precision, efficiency and agility, and gain unmatched visibility, quality, and control.
Is Plex the right fit for you? Let us help you make that determination!
Implementations
-
We offer a proven discovery methodology that accelerates the implementation process and minimizes costly scope changes by utilizing value stream mapping.
-
We take the time to understand your business processes, culture, and objectives to ensure Plex is configured in an optimal manner.
-
Our transparent approach to project management will keep stakeholders aligned and aware of KPIs from milestone attainment to burn rates.
We employ the Plex Critical Path Methodology:
-
We have standardized training plans and work instructions that can be customized to your specific processes.
-
Utilizing a train the trainer approach, our team will ensure that each end-user has a full understanding of how to perform their function in Plex, from the shop floor to the top floor.
-
In addition to the initial Plex implementation, we offer supplemental module implementations when you’re ready to extend the Plex platform.
Training & Support
We offer comprehensive Plex training classes from Shop Floor to Top Floor with specialties such as:
Security
Quality
Finance / Costing
Human Resources
Tooling
Finite
Scheduling
Equipment Maintenance
All of our training classes are complemented by documentation that can be used to support your work instructions.
We'll compliment your team with as little or as much support as you need.
Other services include:
-
EDI as a service
-
New module implementation training
-
Classic to UX transitions
Development & Integration
From custom reports to complimentary applications, our Accredited Plex Development team can create a solution to augment your ERP or MES.
Our team’s capabilities include:
-
SQL & TransSQL for custom reporting and VP Screen creation
-
Custom data visualization with examples such as Daily Health Reviews, Operational Dashboards, and Executive Summaries
-
Data Scientist Development that aids in Data Mining, Storytelling, Forecasting, and Predictive analysis
-
Repetitive and manual work automation
We offer existing solutions such as:
-
Mexico Pack government compliance application
-
Two-tier integration platform that enables Plex to be connected with other ERP systems, financial systems, and/or banks.
-
Custom VisionPlex, IntelliPlex, or visualization reports
-
PLC integration
We have the expertise to create:
-
Custom reports in VisionPlex, IntelliPlex, or using a visualization/dashboard tool like Microsft BI
-
Custom applications
-
Integrations with other software
-
Configure to Order
-
Real-time data reports
Optimizations
We firmly believe that your ERP environment should support your value-added business processes. If your ERP process is creating waste, burdening your people, or not meeting organizational KPIs, we can help analyze and implement improvements. Our optimization approach follows a process improvement methodology of Plan, Do, Check, Act (PDCA):
-
-
Plan - We emphasize the discovery process to ensure a comprehensive understanding of the physical process, ERP process, and overall goals. We perform a gap analysis that enables us to analyze potential solutions and, together with your resources, determine the best solution(s) to implement. We’ll present your leadership with a clear plan of action including timeline and budget.
-
Do - Improvements may be as simple as tweaking an existing configuration or retraining the organization. Other recommendations may include new application implementations, a reconfiguration, or a custom-developed tool.
-
Check - After the recommendations are implemented in an isolated manner, the process should be monitored to validate whether the solution(s) corrected the gaps identified during discovery.
-
Act - Improvements are finalized and rolled out.
-
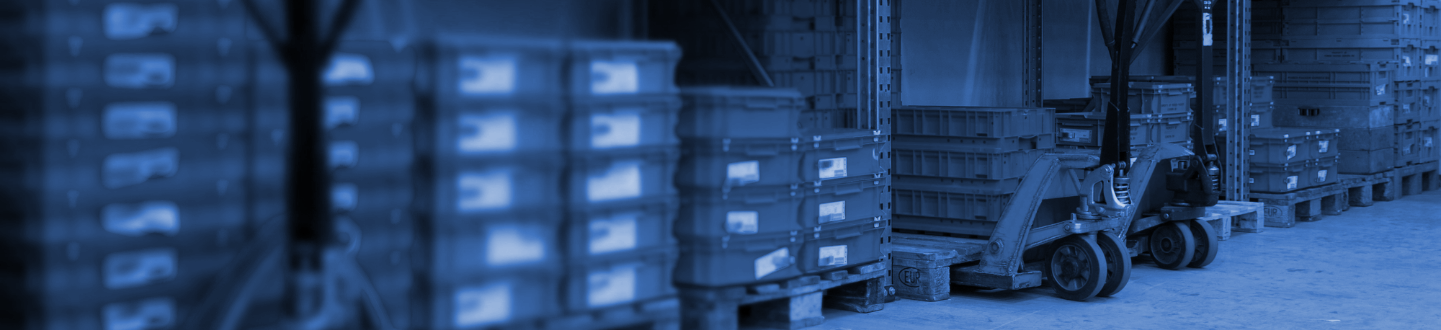