Technology is a core part of many modern businesses. Manufacturing is no exception. In fact, highly successful manufacturers are often dependent on enterprise software to achieve the level of efficiency they need to remain competitive.
Modern manufacturers can use software to help automate key manufacturing processes, improve quality control, and even save time and money on product prototyping.
Why do manufacturers need different types of software? What are some of the enterprise software solutions that they can use?
Why Manufacturers Need Different Types of Software
Software isn’t usually the first thing that comes to mind when people think of manufacturing. Instead, most people think of items like hydraulic presses, steel rollers, arc welders, robot arms, and a hundred other tools of the trade.
However, software can be a key part of improving the quality, consistency, and throughput of different manufacturing processes.
Software can be used to track and automate the ordering of key supplies—such as steel, welding filler, or other raw materials—so that manufacturing processes aren’t disrupted by a shortage of supplies. Computer programs help control factory automation tools to ensure consistent and speedy manufacturing results. Payroll systems help manufacturing plant owners keep track of labor expenses and distribute pay in a fair and equitable manner.
The list of potential uses for software in manufacturing could go on and on.
However, each of these applications requires different kinds of software—a financial tracking software isn’t going to be useful for programming an automated electric arc welder, after all!
So, to ensure the maximum efficiency for individual processes in the business, manufacturers will need different software solutions. But which types of software are the most important for manufacturers to focus on?
RELATED: 5 Ways to Improve Technology Adoption in Your Organization
3 Types of Software Every Manufacturer Should Use
There are countless options for manufacturing automation software and business process software that a manufacturer could choose from—far too many to cover all of them in detail here.
To help you get started on your search for the software that will make the biggest impact on your manufacturing business, here’s a quick list of three types of software that every manufacturer should use:
1. Enterprise Resource Planning Software
Enterprise resource planning (ERP) software is a tool for helping business managers and owners control a wide variety of business processes. This includes things like company finances, supply chain management, productivity reporting, human resource (HR) management, and more.
The right ERP manufacturing solutions can help manufacturers automate and streamline key business operations.
For example, one of the most critical operations for any manufacturer is supply chain management. Many modern manufacturing facilities have moved to a “just in time” model for supply chain management—limiting the number of parts or raw materials they keep in their manufacturing facility to save floor space for more production equipment or other applications.
While this helps the manufacturer maximize their floor space utilization and/or minimize the amount of space they need (reducing costs), it can make the manufacturer more vulnerable to supply chain disruption.
ERP software can help a manufacturer maintain a strong supply chain. By tracking the use rates of certain supplies and generating order reminders (or automatically ordering) when they run low, manufacturers can minimize the risks of a “just in time” supply chain management strategy.
This is just one of the many applications of ERP solutions for a manufacturing company. Another critical use of ERP platforms is for human resource processes. Things like payroll, disciplinary records, employee training programs, and other aspects of HR can help employers:
- Track which employees are performing well;
- Ensure that employee reimbursement follows state and federal guidelines;
- Streamline management for benefits programs (like health insurance) to save time; and
- Set up training programs to ensure employee skills are up to date.
Of course, ERP programs can vary significantly in their capabilities. So, it’s important to choose the right ERP solution (and implementation partner) to meet your needs.
2. 3D Modeling and Simulation Software
3D modeling and physics simulation software programs like Autodesk’s AutoCAD software can be an enormous time-saver for manufacturers. Having the ability to complete a three-dimensional design with computer-aided design (CAD) solutions is already a major advantage for manufacturers.
With 3D design capabilities on a computer, manufacturers can complete designs for enormously complicated parts while minimizing the risk of making errors.
Additionally, some CAD software can be used to virtually test a design before its assembled—simulating use conditions to estimate their effects on the final product. This can be incredibly useful for minimizing prototyping costs and delays.
Traditionally, when making a new part or product, it would have to be physically assembled and put through stress testing. This wastes:
- Resources and labor spent on tooling manufacturing equipment for a limited test run;
- Materials spent on assembling any products that don’t meet specified requirements; and
- Time spent slowly testing materials and products in real-world conditions and refining the design over and over again until a functional product is achieved.
With CAD software and virtual physics simulations, numerous iterations of a design can be tested within minutes or hours instead of days or weeks. Also, with a physics simulation report, designers can determine the exact cause of failure with ease—allowing them to refine the design to address that specific failure cause. This helps speed up the design process even further.
3. Factory Automation Software
Factory automation is crucial for ensuring safety, speed, and consistency for modern manufacturing processes. However, automated manufacturing tools need software to control their operations.
Most manufacturing machines come with their own software for managing their operation. However, that software needs to be integrated with the manufacturer’s workflows to ensure smooth operation. Some manufacturers may even need to develop custom software to integrate new machinery into their manufacturing workflows.
After all, a new steel bending machine won’t be much help if it doesn’t achieve the correct angle in a steel bend. Also, welders won’t help if they’re welding the wrong spot on a part. Having compatible automation software that can help machines correctly follow CAD design files is important for achieving positive results.
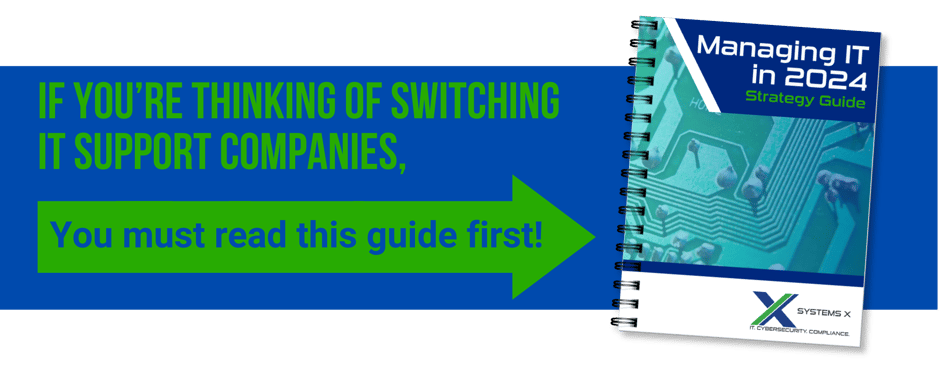
Fill Your Technology Gaps ASAP!
Does your manufacturing facility have a critical technology gap that it needs to fill as soon as possible? Reach out to the experts at Systems X for help! Our team of IT specialists can help you run an IT gap analysis to identify key opportunities so you can connect your business with what’s next in manufacturing.